Filter Bags for the Cement Industry
Increased environmental regulations, such as NESHAP, are forcing cement producers to comply with strict measures for emissions control. GORE® Filter Bags ensure reliable, continuous compliance with membrane-based filter technology proven to increase airflow and productivity.
Contact Us
United States
+1 800 437 5427
Australia
+61 2 9473 6800
Canada
+1 800 437 5427
Central America
+52 81 8288 1281
China
+86 21 51728299
France
+33 (0)1 56 95 65 65
Germany/Austria/Switzerland
+ 49 89 4612 2211
India
+ 91-22-67687000
Italy
+ 39 045 620 9250
Japan
+ 81-3-6746-2572
Korea
+ 82 2 393 3411
Mexico
+52 81 8288 1281
Netherlands
+31 (0) 135 07 47 00
Scandinavia
+ 46 31 706 7800
Singapore
+ 65 6733 2882
Spain
+ 34 93 480 6900
South America
+ 55 11 5502 7800
South Africa
+ 27 11 894 2248
Taiwan
+ 886 2 8771 7799 x28731
United Arab Emirates
+971 2 4437749
United Kingdom
+ 44 1506 460123
Russia
+ 49 89 4612 2211
Overview
Emissions control is a hot topic in the cement industry. Cement plants are driven by throughput, but if they fail to comply with the new NESHAP (National Emission Standards for Hazardous Air Pollutants) regulations, production could be stopped immediately, introducing a slew of cost factors that affect plants’ bottom line.
What’s more challenging for cement plants, and in particular cement baghouses, is how compliance is calculated: with the MACT (Maximum Achievable Control Technology) approach, which sets compliance limits in line with the top 12% of plants. Plant compliance is calculated not at a given moment, but on a 30-day rolling average.
Prior to NESHAP, plants had to prove their compliance based on annual tests. The MACT approach to setting the new limit at the average of the best 12% is a significant change, and the 30-day rolling average makes it even more challenging.
This is why cement producers around the globe trust GORE® Filter Bags. Once installed in pulse jet or reverse air baghouses, our specially designed cement industry filter bags remain reliable, providing unconstrained operations while keeping plants comfortably and continuously compliant. In addition, Gore’s system approach to filtration process optimization includes our technical support for the lifetime of the filter bags.
As industry and baghouse needs have evolved, Gore has introduced new developments in filtration technology that deliver industry-leading performance and reliability. Gore’s latest innovation - GORE® LOW DRAG Filter Bags - allows cement plants to meet emission standards and increase throughput while reducing the costs associated with their dust collectors. GORE® Low Emission Filter Bags are seam-taped to block emissions, ensuring cement plants meet NESHAP and other regulations. GORE® DeNOx Catalytic Filter Bags are designed to destroy NOx and NH3 at levels similar to an SCR tower, but at a much lower investment cost. The GORE® Mercury Control System (GMCS) is a unique fixed sorbent system for capturing elemental and oxidized gas phase mercury from flue gas streams and reduces SO2 concentrations.
Regardless of the Gore solution you choose, and which part of your process it is in, our filtration solutions require virtually no process changes and are easy to install. Watch this video to see how easy it is to install GORE Filter Bags.
The three key filtration factors
Baghouse operators choose their filter bags based on a selection of primary and secondary factors. First and foremost: performance on particulate collection. Will it meet the needs of the application and ensure compliance? Energy costs, which derive from the filter bag material’s resistance to flow (differential pressure), are the second deciding factor. As particular builds up, resistance increases and the fans have to work harder, pushing up energy consumption. Finally, as the filters wear and develop holes, or if the fabric becomes blinded by particulate build-up, the filter bag reaches the end of its life. Expected filter life is, of course, a deciding factor when baghouse operators are selecting a preferred filter media, but it is defined by the first two. Gore filter bags provide just the right balance of:
- extremely high filtration efficiency
- very low resistance to flow
- and extremely long filter life.
These qualities make our filter bags highly durable and reliable through each cleaning cycle, resulting in a long product life overall. Typically, our filter bags will provide five-year effective filter bag life in a pulse jet cement kiln baghouse. Because our bags operate consistently for longer, they don’t need to be replaced as often — equaling lowered maintenance costs, increased yield and greater productivity. Additionally, they are proven to operate with less pressure drop, requiring less energy from the main kiln baghouse fan.
This amounts to lower overall cost of ownership.
Reducing the total cost of ownership
GORE LOW DRAG Filter Bags incorporate an entirely new class of membranes, which provide a fundamentally more cleanable surface and the ultimate baghouse filter design. The resulting lower baghouse differential pressure can either lead to higher airflow during operation or a reduction in fan energy consumption. This material is a game changer for bag filters in cement plants.


Cement producers can benefit from GORE LOW DRAG Filter Bags in multiple ways:
- Reduce fan energy costs
- Increase O2 availability in kiln
- Potentially increase use of alternative fuel
- Reliably meet emissions regulations
- Lowering total cost of ownership
Check out these scenarios:
Scenario 1 |
Production is limited by airflow constraints through the kiln? Increase airflow and use this additional airflow for higher clinker production rates. |
Scenario 2 |
Burning alternative fuels and limited by the amount of fuel burnt due to a shortage of available O2? Increase airflow and utilize this airflow to increase alternative fuel utilization. |
Scenario 3: |
Can’t utilize additional airflow for production increases or alternative fuel increases? Reap the benefit of significant fan energy savings. |
Scenario 4 |
Problem spots in the baghouse due to localized failures or abrasion? Permanently remove filter bags from these areas of the baghouse, while increasing performance. |
GORE LOW DRAG Filter Bags are available for reverse air and pulse-jet baghouses.
Controlling particulate emissions
Though each of our standard filter bags is proven to capture up to 99.99% of emissions, we have a new product especially effective at helping cement plants comply with NESHAP.
GORE Low Emission Filter Bags are especially designed for dust control in the cement industry. They have a PTFE-based seam tape ideal for cement dust control measures, as it makes it virtually impossible for dust to leak through the stitch holes. Studies show that dust emissions from the cement industry spike with each pulse of your cleaning system. GORE Low Emission Filter Bags don’t let dust through despite the constant pulsing — eliminating those emissions spikes, reducing your baseline emission level, and even extending bag life.

GORE Low Emission Filter Bags have a PTFE-based seam tape that makes it virtually impossible for dust to leak through the stitch holes. Gore’s new seam tape does not crack or split.
As the industry has evolved, other industrial filter bags have adopted membrane-based seam tape on their filters and technologies for cement dust control — but the Gore membrane remains ahead of the curve. Other seam tapes tend to crack and split during pulsing, eventually exposing stitch hole leak paths after 12–18 months. Our proprietary membrane remains mechanically robust, keeping emissions under control for the life of your cement filter bags while increasing your total amount of dust collection.
To find out if GORE Low Emission Filter Bags are right for your application, please contact us.
Controlling NOx
In some areas of the world, cement producers must also follow regulations for the control of NOx. To meet these regulations, we recommend GORE DeNOx Catalytic Filter Bags, which are specifically designed to destroy NOx and NH3.
These bags allow plants to achieve NOx and NH3 levels similar to an SCR tower, but at a much lower investment cost. They combine an outer-layer filter bag for particulate removal with a catalyst insert for NOx and NH3 reduction. And there’s very little installation or maintenance involved — in most cases, you just need to replace your current filter bags with GORE DeNOx Filter Bags.

GORE DeNOx Catalytic Filter Bags can be easily installed and implemented just by replacing your filters.
To find out if GORE DeNOx Filter Bags are right for your application, please contact us.
Mercury Capture
Based on a novel Sorbent Polymer Composite (SPC) material, the GORE Mercury Control System provides both high efficiency and a high capacity for removing elemental and oxidized mercury from flue gas streams, and reduces SO2 concentrations.
There is no impact on the final product – the finished cement remains essentially mercury-free and carbon-free. By continually removing mercury from the process, it does not continually concentrate in the CKD. This eliminates the need for Dust Shuttling or Dust Wasting and their associated process changes. The kiln dust can be completely recycled back into the process to maximize clinker yield as is standard for the industry. There is also no need to worry about the logistics and safety of transporting and storing large amounts of powdered sorbents.

The SPC composite captures and sequesters elemental and oxidized mercury while converting SO2 to liquid sulfuric acid.
Why Gore?
As the leading developer of high quality, reliable filtration products for baghouses in the cement industry, we have listened to our customers and considered industry needs when developing solutions that truly address what cement producers face each day.
Gore was the first to develop PTFE-based membrane filters, which are proven to increase airflow and capture up to 99.99% of harmful particulates that pass through a baghouse. With their PTFE membrane and robust construction, our filter bags deliver high performance — and value — while ensuring your plant meets all environmental regulations.
When analyzing Gore’s filtration products for use in your filtration system, we encourage you to consider 3 important factors:
- our truly innovative products which offer filtration performance that you will not find elsewhere
- our proven product reliability
- our unique system approach to filtration process optimization, which includes our technical support for the lifetime of the filter bags
These three attributes enable Gore’s solutions to deliver the lowest total cost of ownership available in a filtration system.
Reliability
Our reputation for reliability is founded on two things: experience and high-quality materials. We use ePTFE (expanded polytetrafluorethylene) to make all our filter bag membranes. This incredible material is:
- chemically inert
- resistant to extreme temperatures
- hydrophobic
- mechanically tough
Gore was the first to develop membrane-based filters for cement baghouses; today, the membranes in our filters simultaneously capture the most miniscule particulates while allowing a high rate of airflow. Regardless of the materials used to fuel your kilns, we deliver consistently high airflow over the lifetime of the filter bags.
The cement industry demands ever-more effective air pollution control systems, and we have risen to this challenge. We’ve worked diligently to improve our filtration product designs and deliver a product that exceeds all expectations. Form, fit and function have all been overhauled to create a filter bag that is highly durable, outlasting competitor’s filter bags, and providing our customers with lower maintenance costs, reduced downtime and a lower total cost of ownership.
Our consistently high-quality bags are the result of strict production and testing procedures, followed by our worldwide manufacturers.
The result? Filter bags that go beyond the required standards – not only immediately after installation, but for 5 or more years of operation.
System approach
From our perspective, we don’t want to just sell you the filter bags and leave you to it. We want you to get the most from them. That’s why we take a system-wide, partnership approach to every contract.
As part of our system approach, we:
- determine, design and manufacture the filter bags that fit your specific application and process
- analyze and optimize your total system performance
- provide technical support and troubleshooting for the lifetime of the filter bags
So, when you buy filter bags from Gore, you get a partnership that lasts the lifetime of the bags, going beyond bag design and installation to process and flow optimization. Our goal is to see you achieve the best productivity without sacrificing compliance. And because we know not everyone has filtration experts on staff, we’re also here to help with day-to-day troubleshooting if you experience any problems related to your filter bags.
What Do Filter Bags Cost?
Purchase price is just one of the factors that contributes to the total cost of your filter bags. When you’re deciding on a product, you should also consider the other costs that will come into play over the life of the bag. This includes the cost of installation, but also maintenance and cleaning costs, energy costs for the baghouse fan, stack testing and CEM monitoring costs, and of course all this should be weighed against how long the bags are expected to last.
GORE Filter Bags are designed to provide the lowest cost of ownership when compared to other brands, by combining:
- superior membrane laminate
- robust filter bag design and construction
- unique system approach optimized for your baghouse
- technical support for the life of your filter bags
- and the reliability our customers come to expect from Gore.
If you’d like to get an idea of how much you could save by switching to GORE® Filter Bags, get in touch.
Success Stories
Cement producers have found success using GORE Filter Bags to maximize their productivity while keeping emissions under control. Learn a few of the stories behind their success.
Global Cement Producer
A global cement producer was operating two inefficient wet process cement kilns with an approximate total production of 1.7 million tons per year. Recently, the plant embarked on a major modification project, replacing the two kilns with a single state-of-the-art preheater/precalciner kiln capable of producing approximately 2.8 million tons per year.
In addition to boosting efficiency with this modification, the plant aims to increase its emissions control through a Fives TGT® baghouse and GORE Filter Bags. To date, we have successfully partnered with Fives Solios on over 20 kiln baghouses within the North American cement industry.
This particular plant needs to meet NESHAP and New Source Performance Standards (NSPS) regulations with a federal limit of 0.02 pounds per ton of clinker emission level via the Continuous Parametric Monitoring System (CPMS). To meet these standards, the plant will install a brand-new Fives TGT baghouse with significant portions of the clean air plenum manufactured from stainless steel construction to prevent corrosion. The baghouse will be equipped with GORE Low Emission Filter Bags, whose ePTFE seam-tape construction positions the plant to remain confidently compliant with its strict operating limits.
Eco-Friendly Cement Plant
Our customer runs progressive and environmentally friendly cement plants. To accomplish this, they rely on GORE Filter Bags, the lowest risk way to optimize system performance, meet emissions targets, and see immediate and long-term cost savings.
With our filter bags in place, our customer has exceeded emissions goals and reduced costs. Says a process engineer, “GORE Filter Bags allow us to meet aggressive environmental standards without sacrificing productivity.”
North American Supplier of Construction Materials
We provide GORE Filter Bags to one of North America’s largest suppliers of diversified construction materials. Our bags have optimized system performance at a low risk. GORE Filters ensure maximum productivity now, plus total cost reductions over the life of their kiln exhaust system.
Our customer has been very pleased with its production increases resulting from the installation of GORE Filter Bags. The director of engineering says: “GORE Filter Bags allow us to keep up with production demands without having to add additional capital equipment.”
Product Comparison
Gore produces a wide range of filter bags that vary by material and resistance to temperatures, acid and alkali.
In your cement plant, GORE Low Emission Filter Bags provide extra assurance that you’ll meet NESHAP regulations. The bags are seam-taped to prevent any leaks, allowing them to meet the strictest emissions regulations while providing the same level of quality and reliability as our standard filter bags.
In Europe, cement plants are also regulated for NOx output. GORE DeNOx Catalytic Filter Bags are designed to destroy NOx and NH3. These easy-to-install bags enable plants to achieve NOx and NH3 levels similar to an SCR tower, but at a much lower investment cost.
Compare our range of filtering solutions, and contact us to discuss which solution is right for your industrial application.
To get started, we’ll need to know:
- filterbag size, current material and quantity
- baghouse operating parameters (e.g.: airflow rate, temperature, differential pressure)
- particulate characteristics (describe concentration, particle size, bulk density)
- cleaning cycle parameters (e.g.: pulse jet pressure, cycle time)
GORE Baghouse Filter Products Most Commonly Used in the Cement Industry
Product:
Acrylic Felt,
475 g/m2 (14 oz/yd2)
Continuous Operating
Temperature:
127ºC (260ºF)
Acid Resistance:
Excellent
Alkali Resistance:
Good
Product:
Fiberglass Fabric
Acid-Resistant
339 g/m2 (10 oz/yd2)
Continuous Operating
Temperature:
260ºC (500ºF)
Acid Resistance:
Very Good
Alkali Resistance:
Fair
Product:
Fiberglass Fabric
Coated with
Polytetrafluoroethylene
746 g/m2 (22 oz/yd2)
Continuous Operating
Temperature:
260ºC (500ºF)
Acid Resistance:
Very Good
Alkali Resistance:
Fair
Product:
Polyester Felt
Anti-Static
475 g/m2 (14 oz/yd2)
Continuous Operating
Temperature:
135ºC (275ºF)
Acid Resistance:
Fair
Alkali Resistance:
Fair
Product:
SUPERFLEX Fabric
614 g/m2 (18.1 oz/yd2)
Continuous Operating
Temperature:
260ºC (500ºF)
Acid Resistance:
Very Good
Alkali Resistance:
Fair
Product:
Cartridge
Spunbonded Polyester
271 g/m2 (8 oz/yd2)
Continuous Operating
Temperature:
113ºC (235ºF)
Acid Resistance:
Fair
Alkali Resistance:
Fair
Product:
Polyimide/ePTFE Felt
830 g/m2 (24.5 oz/yd2)
Continuous Operating
Temperature:
260ºC (500ºF)
Acid Resistance:
Very Good
Alkali Resistance:
Very Good
Product:
PTFE Felt
830 g/m2 (24.5 oz/yd2)
Continuous Operating
Temperature:
260ºC (500ºF)
Acid Resistance:
Excellent
Alkali Resistance:
Excellent
Resources
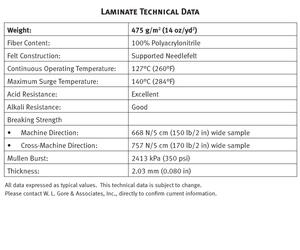
Data Sheet: Acrylic Felt GORE® Filter Bag 475 g/m2 (14 oz/yd2)
Data Sheets, 109.62 KB
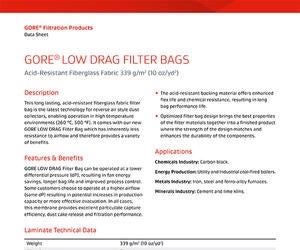
Data Sheet: GORE® LOW DRAG Filter Bags 3170, Fiberglass Fabric, 339 g / m2 (10 oz / yd2)
Data Sheets, 52.44 KB
View all Resources for Industrial Baghouse Filters (Cement Industry)
FOR INDUSTRIAL USE ONLY
Not for use in food, drug, cosmetic or medical device manufacturing, processing, or packaging operations.