GORE® Packaging Vents for Agricultural Applications
During distribution and storage, improperly vented agricultural products like fertilizers and pesticides can bloat, collapse or leak — putting customers at risk and resulting in unplanned costs. GORE Packaging Vents use superior membrane structures to enable airflow and prevent leaks for even the most highly-concentrated liquids.
Contact Us
United States
+1 800 542 2624
Australia
+61 2 9473 6800
Benelux
+49 89 4612 2211
China
+86 21 5172 8299
France
+33 1 5695 6565
Germany
+49 89 4612 2211
India
+91 22 6768 7000
Italy
+39 045 6209 240
Japan
+81 3 6746 2570
Korea
+82 2 393 3411
Mexico
+52 81 8288 1281
Scandinavia
+46 31 706 7800
Singapore
+65 6733 2882
South Africa
+27 11 894 2248
South America
+55 11 5502 7800
Spain
+34 93 480 6900
Taiwan
+886 2 2173 7799
United Kingdom
+44 1506 460123
Overview
Agricultural chemical packaging needs to be ventilated.
It’s especially critical to use vented agricultural containers for high-offgassing products, and those whose natural variations provoke varying rates of fermentation and gas release:
- Agricultural liquid fertilizers
- Pesticides
- Biostimulant products
Without the appropriate vents, agricultural containers could collapse, bulge or leak when exposed to changes in altitude or temperature. Pallets could collapse. Labels could be ruined and as a result important safety information can be potentially illegible. Consumers could be exposed to leaked chemicals, while agricultural packaging manufacturers could experience decreased profits due to lost productivity and unsatisfied customers.
Gore’s packaging vents minimize these risks for even the most highly concentrated chemical formulations, and we provide vents that meet the stringent ADR and DOT standards.
GORE PACKAGING VENTS MINIMIZE RISKS FOR AGRICULTURAL CONTAINER SUPPLIERS AND END-USERS
Our portfolio of vents for agricultural products packaging meet stringent ADR and DOT standards, and are designed to reliably protect the integrity of containers that bear the most challenging contents:
- biostimulant formulations
- liquid fertilizer packaging
- highly-concentrated chemical formulations

GORE Packaging Vents protect agricultural packaging from deformation, leaks and label damage.
Two ways GORE Packaging Vents protect package integrity
Why Vent?
From manufacturers of liquid chemicals or caps and containers, through transport and storage, to end-users, everyone benefits from effective venting, because it:
- Safely equalizes pressure differentials that could cause containers of liquid chemicals to deform, leak or burst.
- Prevents damage to packaging and labeling, and the associated damage to brand reputation.
- Minimizes the risk of time-consuming and costly efforts to deal with returns, spills or clean-ups due to leaky or damaged containers.
GORE® Packaging Vents minimize all these risks for all types of packaging in agricultural applications. They reliably and continuously equalize pressures, to minimize the potential for leaks and maintain the integrity of containers and their contents. When container integrity is paramount, GORE Packaging Vents are the solution
The problem — container deformation that can lead to leaks or bursting — arises when the pressures inside and outside the container are not balanced.
GORE Packaging Vents safely and reliably relieve these imbalances, whatever their source:

Without venting, pressure build-ups can cause a container to bloat, leak or burst, while under-pressures can cause container collapse.
Active ingredients in chemical packaging applications can off-gas (release gases within the container), or they can scavenge (consume) free oxygen within the container.
- Off-gassing will build up pressure within the container.
- Oxygen scavenging will create under-pressure within the container

Without venting that continuously re-balances the internal and external pressures, the dispensing container may collapse.
Unless it is properly vented, industrial fluid packaging that provides a dispensing function is always vulnerable to collapse. That’s because the act of dispensing automatically creates an under-pressure within the container, and that under-pressure recurs with each use.

Sudden or extreme changes in the external environment will accelerate the deformation.
During distribution or storage, industrial chemical or cleaner packaging is exposed to changes in the external environment. These changes (increasing or decreasing temperatures or altitudes) create pressure imbalances that can cause unvented or inadequately-vented containers to bloat or collapse.
Applications
Packaging of agricultural produce requires special care — as does packaging of agricultural products with active ingredients. In each case, the contents require special protection to reach the end-user undamaged. Gore has a venting solution for all types of materials used for packaging agricultural products, from consumer spray bottles to jerry cans and IBCs.
The UN Orange Book* recommends venting for any formulation that could cause package deformation. Highly-concentrated pesticides or fertilizers produce higher levels of off-gassing or oxygen-scavenging. Venting protects their packaging from deformation, leaks and label damage.
Examples of agrochemicals that require venting:
- Organic/inorganic fertilizers
- Pesticides
- Biostimulant formulations
- Gardening liquids
Discover what else GORE Packaging Vents can do:

GORE® Packaging Vents perform reliably to minimize risk in a wide variety of chemical packaging applications.
HAZARDOUS CHEMICALS AND INSTITUTIONAL CLEANERS
According to the U.N. Orange Book*, if a dangerous good is vented, no leakages are allowed. Packaging engineers must address this need for leak-proof yet breathable packaging to protect the container and its contents through the whole product life cycle.

For today’s more highly-concentrated household chemical formulations, venting is increasingly required. Retail environments offer customers plenty of choices, so they don’t hesitate to reject deformed, leaky or label-damaged packages. Reliable venting is the key to successful packaging and satisfied customers.
* United Nations Recommendations on the Transport of Dangerous Goods Model Regulations, a guidance document to harmonize transport regulations for dangerous goods. Most dangerous goods regulations (ADR, IMDG Code, IATA and other national regulations) are based on the U.N. Orange Book.
Product Portfolio
Choose GORE Packaging Vents to prevent leaks and deformations, and enhance agricultural container integrity. Both Plug-In Vents and Liners are available in multiple sizes and performance options. All incorporate the GORE Membrane, to provide breathable barrier protection for both the container and its contents.
Gore’s Plug-In Vents are designed for use with hazardous chemicals, agrochemicals, biostimulant products, organic fertilizers, institutional cleaners and household chemicals.
They readily withstand harsh chemicals and rugged use: They comply with U.N. Orange Book test standards, including the Stacking Test and Drop Test, as well as Dangerous Goods regulations like ADR and DOT.
- Available for container sizes from very small to 1,500 liters
- Suitable for industrial drums, jerry cans and IBCs as well as consumer containers
- Easy to integrate into container closures via press-fit or snap-fit
![]() |
D38 / D17 / D15 |
![]() |
D15 Converse |
![]() |
D10 |
![]() |
D3 |
See full details for each Gore Plug-In Vent
For complete details, please download our new GORE Packaging Vents Portfolio Data Sheet.
Gore Foam Liners and Gore Pulp Induction Liners easily convert non-vented containers into vented containers — without modifying the existing cap or closure!
- Designed for cap-thread venting or hole-in-cap venting
- Available in single- or multi-up rolls in a range of widths
- Cut parts can also be provided
![]() |
Gore Foam Liners
|
![]() |
Gore Pulp Induction Liners
Gore Pulp Induction Liners provide reliable venting and tamper-evidence for agrochemicals including organic biostimulants.
|
For complete details, please download our new GORE Packaging Vents Portfolio Data Sheet.
Why Gore?
When you seek solutions for packaging that bloats, collapses or leaks, there are compelling reasons to make Gore your preferred partner:
- >25 years of partnering with leading chemical and cap & container manufacturers on applications including industrial chemicals and cleaners, agrochemicals, and institutional and household cleaners.
- Technical expertise in the properties and behavior of off-gassing/oxygen-scavenging chemicals, and in the ways fluid viscosity and surface tension affect venting.
- Development of proprietary testing methods such as Residual Airflow and LEP, which enable us to quantify our vents’ response to real-world challenges.

The roll-off optimized GORE Membrane enables rapid airflow recovery after contact with high-viscosity or low surface-tension household chemicals.
- We continue to develop new and proprietary membrane technologies, even as we evolve and improve existing ones.
- Our membrane structures and properties can also be customized for specific customer needs or applications.
- We design and manufacture every vent we sell, and — unlike competitors — also every membrane that goes into them.
- Customers worldwide rely on our robust global supply chain for ready access to the products and support resources they need.

Gore’s global supply chain ensures our customers will be able to access needed products as well as our sales and engineering support.
- GORE Packaging Vents pass rigorous approval tests for dangerous goods, and meet DOT and ADR standards.
- You’re assured of consistent product quality because our in-line manufacturing tests verify the structural and membrane integrity of each individual vent.
- Three Series of Plug-In Vents enable 100% traceability, because each vent has an individual laser-marked tracking code. All other vents offer lot-level traceability.

Individual laser-marking is just one example of Gore’s commitment to excellence in both product quality and service.
Resources

GORE® Packaging Vents: For Chemicals and Cleaners
Data Sheets, 1.78 MB
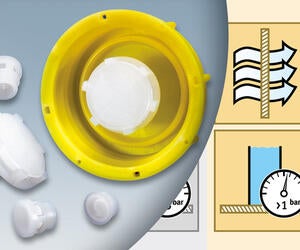
Why Choose GORE® Packaging Vents?
Brochures, 566.43 KB
View all Resources for GORE Packaging Vents for Agricultural Applications
FOR INDUSTRIAL USE ONLY
Not for use in food, drug, cosmetic or medical device manufacturing, processing, or packaging operations.