GORE® GR Sheet Gasketing
Exceptionally resistant to creep, cold flow and aggressive media, this 100% expanded PTFE gasket sheet reliably seals steel piping and equipment.
Contact Us
United States
+1 800 654 4229
Australia
+61 2 9473 6800
Brazil
+55 11 5502 7800
China
+8621 5172 8299
France
+33 1 56 95 65 65
Germany
+49 89 4612 2215
Hong Kong
+852 2622 9622
India
+91 22 67687000
Italy
+39 045 6 20 92 50
Japan
+81 3 6746 2600
Korea
+82 2 393 3411
Netherlands
+31 13 507 47 00
Poland
+48 22 6 45 15 37
Scandinavia
+46 31 706 78 00
Singapore
+65 6733 2882
South Africa
+27 71 467 7710
Spain
+34 93 4 80 69 00
United Arab Emirates
+971 2 5089444
United Kingdom
+44 1506 46 01 23
Overview
GORE GR Sheet Gasketing is designed to outperform both conventional (filled and skived) PTFE and other ePTFE gasketing in steel piping and equipment.
GORE GR Sheet Gasketing has the chemical resistance of conventional PTFE sheet gasketing without the creep and cold flow commonly associated with that material. GORE GR Sheet Gasketing is stronger and more dimensionally stable than other ePTFE gaskets. It is highly conformable to rough or irregular sealing surfaces, and compresses into an extremely tough gasket that creates a tight, long-lasting seal.
Whether you use a single sheet to make one very large (1.5 m x 1.5 m) gasket or multiple smaller pipe flange gaskets, GORE GR Sheet Gasketing is a versatile, single-solution material for both standard and custom gasketing shapes and sizes.
Applications
GORE GR Sheet Gasketing is a tough, dimensionally-stable and chemical-resistant gasket sheet for sealing steel pipe and equipment flanges in a wide range of applications and process conditions. It reliably seals flanges with rough surfaces, and is ideal for flanges that require complex gasketing shapes or larger gasketing sizes.
Processes utilizing highly-aggressive media, as in:
- Chemical processing
- Pulp and paper manufacturing
- Mining and minerals
- Semiconductor manufacturing
- Power generation
Large, complex or non-standard steel equipment flanges in:
- Columns
- Reactors
- Turbines
- Heat exchangers
- Tanks
- Pipe flanges
APPLICATIONS FOR GORE GR SHEET GASKETING

GORE® GR Sheet Gasketing performs durably across a range of challenging applications, reliably sealing steel flanges that demand a chemical-resistant gasket material or a high-temperature gasket sheet.
Performance Benefits
Whether your application requires long-term reliable sealing, a high-temperature gasket or chemical-resistant gasketing, GORE GR Sheet Gasketing offers all of that — as well as a number of additional performance advantages.
WHY CAN GORE DELIVER SUPERIOR SHEET GASKET PERFORMANCE PROPERTIES?
Proprietary, patented technology
Gore’s 100% expanded PTFE sheet material is specially engineered for high performance. Our patented manufacturing technology creates an ePTFE sheet with the highest degree of expansion available. Other ePTFE material has many un-expanded nodes. The increased expansion of GORE GR Sheet Gasketing gives it superior tensile strength and dimensional stability, creating significant performance advantages in demanding applications.

Gore’s ePTFE is more highly-expanded and consistent than other ePTFE, for superior performance in demanding applications.
Superior resistance to creep and cold flow
GORE GR Sheet Gasketing has greater tensile strength, so it retains greater dimensional stability in-use — in both size and width — than any other PTFE-based or ePTFE flange gasket sheets.
- Because its creep-resistance is better than that of any other PTFE-based gasket, GORE GR Sheet Gasketing maintains a greater percentage of bolt load in operation, providing a more reliable solution for making flange connections, especially in thermal cycling and high heat conditions.
- The width of GORE GR Sheet Gasketing also remains more dimensionally stable, avoiding gasket intrusion into the pipe bore which can negatively affect process performance.
- Along with providing a larger window for blowout safety, the dimensionally-stable seal can also increase process uptime and reduce maintenance costs associated with gasket re-torque and replacement.

Tests show that, even in high heat, GR Sheet Gasketing is more dimensionally stable than other PTFE or ePTFE gasketing. (Tested at 34.5 MPa (5000 psi) load, 230 °C (446 °F) for 15 minutes.)
Exceptionally reliable sealing performance
Crush-resistance tests show GORE GR Sheet Gasketing excels at withstanding the extreme conditions of industrial flange sealing. It delivers a wider safety margin of seal reliability, both at installation and in operation at elevated temperatures.
Chemically-inert GORE GR Sheet Gasketing seals durably, whether in strong alkali-, acid- or solvent-based process systems. It resists all media (pH 0-14) except for molten/dissolved alkali metals and elemental fluorine.

GORE GR Sheet Gasketing creates a durable, reliable seal that offers a wider safety margin than other ePTFE at installation and under harsh operating conditions.
Greater consistency, for fewer problems
The consistency and precision of Gore manufacturing processes give GORE GR Sheet Gasketing a much more uniform distribution of mass than other ePTFE sheets. This promotes a more uniform and reliable seal.
Unlike skived or filled PTFE, GORE GR Sheet Gasketing readily conforms to common flange imperfections. Gore’s flange gasket sheet can eliminate the need for flange resurfacing, expand the window of applicability and create a highly reliable initial seal, so start-ups can be more trouble free.

Gore manufactures a more consistently dense and conformable product, so GORE GR Sheet Gasketing can seal rough or damaged flanges more reliably.
Technical Specifications
Test Data
Gasket Design Factors
CERTIFICATES & APPLICATION INFORMATION
Resources
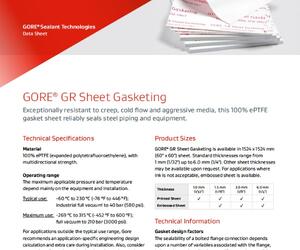
Data Sheet: GORE® GR Sheet Gasketing
Data Sheets, 112.8 KB
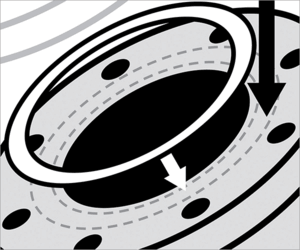
Installation Guide: GORE® GR Sheet Gasketing
Installation Guides
GORE® GR Sheet Gasketing conforms to the US FDA 21CFR and EU directive EC 1935/2004 requirements relating to food contact. Declaration of Compliance is available upon request.