GORE® Gasket Tape Series 1000
Easily and reliably seal glass-lined steel to contain aggressive media, protect equipment, and reduce emissions.
Contact Us
United States
+1 800 654 4229
Australia
+61 2 9473 6800
Brazil
+55 11 5502 7800
China
+8621 5172 8299
France
+33 1 56 95 65 65
Germany
+49 89 4612 2215
Hong Kong
+852 2622 9622
India
+91 22 67687000
Italy
+39 045 6 20 92 50
Japan
+81 3 6746 2600
Korea
+82 2 393 3411
Netherlands
+31 13 507 47 00
Poland
+48 22 6 45 15 37
Scandinavia
+46 31 706 78 00
Singapore
+65 6733 2882
South Africa
+27 71 467 7710
Spain
+34 93 4 80 69 00
United Arab Emirates
+971 2 5089444
United Kingdom
+44 1506 46 01 23
Overview
Chemical processors use glass-lined steel pipe and equipment to deal with aggressive media under demanding conditions. Yet the inherent demands of such systems can make it challenging to maintain a tight, lasting seal and prevent leaks that can pose hazards to the equipment, and to the working environment.
GLASS-LINED STEEL SEALING CHALLENGES
- High temperatures
- Alternating system pressures
- Limited gasket loads
- Deviations in flanges / sealing surfaces
GORE GASKET TAPE SERIES 1000
GORE Gasket Tape Series 1000 addresses all the challenges of reliably sealing large glass-lined flanges. Made of 100% expanded PTFE (ePTFE), this highly conformable sealant tape is chemically inert, and highly resistant to creep, cold flow and clamp-force loss. Its proprietary barrier core maintains an extra-tight seal even at low loads.
Highly creep resistant, to maintain gasket load
Highly conformable, to seal surface deviations
Barrier core for extra tightness at low loads
Chemically-inert 100% ePTFE protects full width of flange

Applications
GORE Gasket Tape Series 1000 offers the performance and versatility to reliably seal a range of industrial glass-lined equipment, in diverse applications with harsh process conditions.
- Processes that use highly-aggressive media, for example, in the chemical processing or mining and minerals industries.
- Any glass-lined columns, mixer vessels, or reactor, storage and receiver tanks with glass-lined steel flanges that are large (≥ DN600/ASME 24”) or non-standard.
APPLICATIONS FOR GORE GASKET TAPE SERIES 1000

GORE® Gasket Tape Series 1000 addresses all the challenges of reliably sealing large glass-lined steel flanges.
Performance Benefits
With Gore’s advanced ePTFE material technology and its proprietary barrier core, our Series 1000 gasket tape enables high-performance, high-reliability sealing.
Why consider ePTFE tape
Unique barrier core technology
- Barrier core engineered to amplify the available load.
- Seals more than 10 times tighter than other ePTFE gasket tapes. (Especially important where glass-lined reactor safety is a consideration.)
Outstanding conformability to deviations
- Seals deviations even at low gasket stress.
- Easily passes the bubble test, for trouble-free mechanical completion (MC) or start-up.

Cross section of GORE® Gasket Tape Series 1000 checked with Finite Element Analysis (FEA) model. Red indicates optimal sealing stress.
Optimal form for easy handling
- Gasket can be customized on-site.
- No fabrication lead-time required.
- Convenient spool format simplifies and speeds handling & transport.
- Adhesive backing enables easy installation in ambient temperatures from 2–50 °C (36–122 °F).
- Faster, less complicated shimming tape technique for larger deviations.
- Reduces inventory costs.

Installation temperature window is effective from hot summer conditions to almost freezing surface temperature.
Reliable and long-term seal
- Barrier core creates a tight seal that impedes even highly-permeating media.
- Provides chemical protection across the full flange width (100% ePTFE).
- Tape is engineered to resist creep and clamp-force loss.
- Allows full use of specification range of the glass-lined steel equipment.
- Enables longer maintenance cycles, as demanded by leading chemical producers.

Cross-section shows how well GORE Gasket Tape Series 1000 endures in challenging conditions with aggressive media.
GORE GASKET TAPE SERIES 1000 OUTPERFORMS THE COMPETITION
Technical Specifications
See how fast and easy it is to reliably seal a large flange with GORE Gasket Tape Series 1000: |
Test Data
Certificates & Application Information
Resources
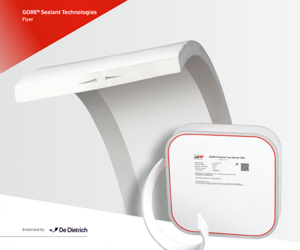
Product Flyer: GORE® Gasket Tape Series 1000
Brochures, 812.69 KB
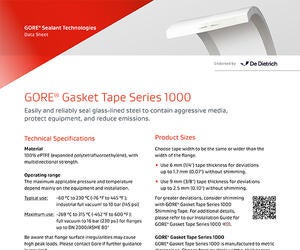
Data Sheet: GORE® Gasket Tape Series 1000
Data Sheets, 210.21 KB
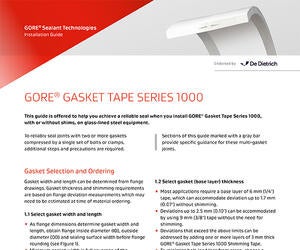
Installation Guide: GORE® Gasket Tape Series 1000
Installation Guides, 489.45 KB
FOR INDUSTRIAL USE ONLY
Not for use in food, drug, cosmetic or medical device manufacturing, processing, or packaging operations.
Follow GORE® Gasket Tape Series 1000