GORE® Gasket Tape Series 500
This exceptionally creep-resistant 100% ePTFE form-in-place gasket tape delivers worry-free high-temperature sealing performance in large steel flanges.
Contact Us
United States
+1 800 654 4229
Australia
+61 2 9473 6800
Brazil
+55 11 5502 7800
China
+8621 5172 8299
France
+33 1 56 95 65 65
Germany
+49 89 4612 2215
Hong Kong
+852 2622 9622
India
+91 22 67687000
Italy
+39 045 6 20 92 50
Japan
+81 3 6746 2600
Korea
+82 2 393 3411
Netherlands
+31 13 507 47 00
Poland
+48 22 6 45 15 37
Scandinavia
+46 31 706 78 00
Singapore
+65 6733 2882
South Africa
+27 71 467 7710
Spain
+34 93 4 80 69 00
United Arab Emirates
+971 2 5089444
United Kingdom
+44 1506 46 01 23
Overview
Sealing large steel flanges in industrial or chemical processing operations can be complicated: factors like aggressive media, thermal cycling, uneven or corrosion-damaged sealing surfaces can compromise seal durability and longevity. While one-piece prefabricated gaskets can be an option, it can be a costly one: as well as price, there can be long lead-times and supply-chain issues to consider.
LARGE STEEL FLANGE SEALING CHALLENGES
- High temperatures / thermal cycling
- Alternating system pressures
- Aggressive media
- Uneven flanges / sealing surfaces
GORE GASKET TAPE SERIES 500
A spool of GORE® Gasket Tape Series 500 provides an immediate, cost-effective solution to sealing challenges that demand reliable performance and extended durability. This high-temperature gasket tape, with its industry-leading creep resistance, is designed to maximize the operational reliability of large-diameter steel flange applications, especially those with thermal cycling.
Applications
GORE Gasket Tape Series 500 creates a high-performance seal that fits any shape, instantly and reliably, to create a tight and long-lasting seal, in diverse applications with harsh process conditions — especially those that require a high-temperature sealing tape.
WHAT IS HIGH-TEMPERATURE GASKET TAPE GOOD FOR?
High-temp gasket tape is ideal for large steel flanges in any processes involving thermal cycling — that is, processes with inherently variable and/or extreme operating temperature ranges.
Thermal cycling affects the coefficient of expansion of the steel flanges and bolt-loads, and as well as the cold-flow and creep properties of the surrounding gaskets. Therefore, processes that involve thermal cycling require a gasket designed to withstand them, in order to maintain the integrity of the seal.
Processes involving highly-aggressive media or thermal cycling:
- Chemical processing
- Pulp and paper manufacturing
- Mining and minerals
- Semiconductor manufacturing
- Power generation
Large and/or non-standard steel equipment flanges:
- Vessel and tank process flanges & manways
- Large-diameter piping
- Heat exchangers
- Baffles
- Non-Standard flanges (rectangular, …)
APPLICATIONS FOR GORE GASKET TAPE SERIES 500

GORE® Gasket Tape Series 500, a high-temp sealant tape, withstands thermal cycling and aggressive media to reliably seal steel flanges in diverse applications.
Performance Benefits
Gore invented form-in-place tape gasketing decades ago. Today, GORE Gasket Tape Series 500 takes high-temperature gasket tape sealing performance and convenience to a new level. This expanded PTFE tape forms to fit any shape, instantly and easily, so that even large flanges are a one-person job.
WHY GORE’S HIGH-TEMPERATURE GASKET MATERIAL OUTPERFORMS ORDINARY PTFE TAPE

GORE Gasket Tape Series 500 excels at maintaining seal integrity on large steel flanges, even when exposed to high temperatures or thermal cycling.
Proprietary manufacturing technology
GORE Gasket Tape Series 500 is made of 100% expanded polytetrafluoroethylene (ePTFE), using a proprietary Gore manufacturing technology that creates a high-temp gasket tape with exceptional sealing reliability, especially on large and irregularly shaped steel flanges.
The expansion of PTFE adds creep resistance and better cold flow resistance, which enables the material to withstand high-temperature applications.
High-temperature sealant tape
GORE Gasket Tape Series 500 is typically used in applications with a temperature range of -60 °C to 230 °C (-76 °F to 445 °F) up to 40 bar (580 psi). If your high-temp flange gasket must withstand non-typical temperature/pressure ranges, Gore can provide guidance and recommendations: please contact us.
Almost twice as creep-resistant
Because of its internal structure, GORE Gasket Tape Series 500 excels at resisting cold flow and creep. Tests prove GORE Gasket Tape Series 500 is nearly twice as effective at resisting creep than other brands of ePTFE gasket tape.

Gore’s Series 500 is almost twice as creep-resistant as other ePTFE gasket tapes. (Data based on EN13555.)
Highly conformable, for added sealing integrity
GORE Gasket Tape Series 500 is also highly conformable, compensating for considerable flange irregularities. The resulting seal is both very tight, and very long-lasting, enhancing overall system reliability and safety.
Preview: Conformability Case History
Chemically inert, to withstand the harshest process media
Made of chemically-inert 100% ePTFE, GORE Gasket Tape Series 500 is versatile enough for use in strong alkali-, acid- and solvent-based process systems. It durably withstands the rigors of harsh chemical processes as it resists all process media (pH 0-14) except molten/dissolved alkali metals and elemental fluorine. Therefore, GORE Gasket Tape Series 500 is a single solution to multiple gasketing needs.

GORE Gasket Tape Series 500 is a time- and cost-saving alternative to ordering, storing and installing very large one-piece gaskets.
Saves time, money and trouble
GORE Gasket Tape Series 500 delivers significant advantages, both onsite and offsite.
It eliminates the lag time, costs and complexities associated with engineering, specifying, procuring, shipping, storing and installing traditional one-piece prefabricated gaskets.
Series 500 delivers exceptionally reliable sealing performance, while making multiple gasketing installations faster, more cost-effective and simpler.
» See how to install Series 500 in just a few quick, easy steps: view our Installation Guide. |
Technical Specifications
Test Data
Gasket Design Factors
Certifications & Application Information
Resources

Data Sheet: GORE® Gasket Tape Series 500
Data Sheets, 112.74 KB
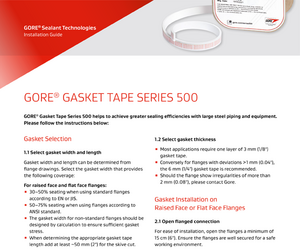
Installation Guide: GORE® Gasket Tape Series 500
Installation Guides, 541.99 KB
FOR INDUSTRIAL USE ONLY
Not for use in food, drug, cosmetic or medical device manufacturing, processing, or packaging operations.