GORE® High Performance Aerospace Wires for Defense Aircraft
For future aircraft electrification needs, our aviation power wires offer the best combination of durability and electrical reliability over time that OEMs and program managers want and need. Without enlarging wire bundle size or adding extra weight, they’re proven to deliver long-term stability, improve safety, increase aircraft availability and reduce total costs.
Contact Us
+1 800 626 7708
Germany
+49 9144 6010
+49 9144 6816 (fax)
UK
+44 1382 56 1511
+44 1382 56 1007 (fax)
Italy
+39 045 6209 209
+39 045 6209 165 (fax)
France
+33 1 5695 6565
+33 1 5695 6401 (fax)
Spain
+34 93 480 6900
+34 93 373 7850 (fax)
Sweden
+46 31 7067800
+46 31 864226 (fax)
China (Beijing)
+86 10 5707 4999
+86 10 5707 4900 (fax)
China (Shanghai)
+86 21 5172 8299
+86 21 6247 9199 (fax)
China (Shenzhen)
+86 755 8359 8262
+86 755 8359 1654 (fax)
South Korea
+82 2 393 3411
+82 2 393 1285 (fax)
Japan
+81 3 6746 2582
+81 3 6746 2571 (fax)
Product Overview
ENSURE RELIABLE AIRCRAFT ELECTRIFICATION
When it comes to aircraft electrification, aircraft wire insulation must be durable enough to ensure reliable EWIS (electrical wire interconnection systems). But electrification requires higher aircraft voltage, which stresses wiring more and causes potential physical damage. Typical insulation materials are often limited in durability and degrade over time when exposed to harsh airborne conditions. You can add extra aerospace wiring insulation for more durability, but it increases wire bundle size and weight, plus adds unwanted aircraft weight.
Gore offers a single optimal solution that OEMs (original equipment manufacturers) and program managers want and need for future military aircraft electrification.
Best Combination of Durability & Long-Term Stability
GORE High Performance Aerospace Wires offer greater mechanical strength and exceptional electrical reliability over time without adding to wire bundle size and weight. They meet higher durability levels for aircraft electrical wire bundles operating in severe airborne conditions. We thoroughly test our wires to meet the most current aircraft wiring standards, like ASTM D3032 and SAE AS4373™.
Our wire insulation is proven to have a higher PDIV/PDEV while displaying higher voltage breakdown and endurance than alternative aerospace wire and cable materials. This unique aircraft wire insulation offers other proven advantages over alternative materials, like resistance to extreme operating temperatures, humidity and harsh chemicals without degrading. And our insulation is proven to resist chafing, abrasion and cut-through failures.
Material Comparison
Review the table below to compare the insulation material in GORE High Performance Aerospace Wires against common insulation materials for aircraft wires and cables.
Keep in mind that current aircraft electrical wiring solutions either contain polyimide or show limitations in physical and electrical properties. The yellow squares indicate good overall results from our abrasion testing. But, the underlying polyimide is quickly exposed, risking degradation, arc tracking and more. Any improvements to these materials in commonly used aircraft electrical wire types to add durability will likely add size and weight.
Critical Attributes | Extruded Fluoropolymer (XLETFE) | PTFE/Polyimide Composite | Gore Engineered Fluoropolymer (EFP) |
---|---|---|---|
Mechanical Durability | ∎ | ∎ | ∎ |
Electrical Durability | ∎ | ∎ | ∎ |
Long-Term Material Stability | ∎ | ∎ | ∎ |
Green = Acceptable/Good
Yellow = Concern/Uncertainty
Red = Unacceptable/Low Performance
Features & Benefits
Unlike common insulation materials, GORE High Performance Aerospace Wires offer unique features that provide long-term stability against challenging environmental factors and aircraft conditions, including:
- low-permittivity, higher PDIV/PDEV material
- temperature-resistant, chemically inert, non-flammable material
- abrasion- and cut-through resistant material
- hydrophobic, non-hydrolyzing material
For system architects and engineers, our aircraft power wires deliver numerous benefits that meet military aircraft electrification needs and requirements, like:
- proven strength against chafing, abrasion and cut-through over wide temps
- resist chemicals or fire for increased aircraft safety and improved system performance
- no degradation over time from hydrophobic, non-hydrolyzing material
- improved electrical durability and less voltage breakdown over time in demanding MEA applications
- greater EWIS reliability, increased aircraft availability and reduced costs
- increased future-proofing with wires that can withstand higher voltage requirements
Get Samples or Buy
Meet all your electrical wire system needs with our single optimal solution that ensures EWIS reliability over time, increases aircraft availability, improves safety and reduces total costs. Confirm the compatibility of our high-performance wire and cable solution in your application by ordering complimentary samples from our selection.
If you want to purchase our aerospace cables and wires, connect with a trusted distributor now. Otherwise, call us today for available qualification test data or to talk about your specific electric aircraft system needs and requirements.
Resources
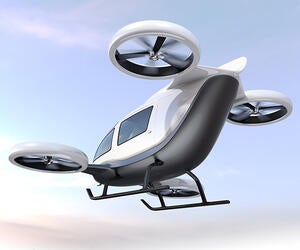
Data Sheet: GORE® High Performance Aerospace Wires
Data Sheets, 1 MB
View all resources for GORE High Performance Aerospace Wires for Defense Aircraft
Recent News
Press Release
Gore Showcases Latest Lightweight Aerospace & Defense Solutions at Paris International Air Show
Posted June 16, 2025
W. L. Gore & Associates, a global leader providing solution-oriented innovations that include future materials for aerospace, is proud to showcase its latest lightweight innovations at the Paris International Air Show, held from 16 – 22 June at Le Bourget, France.
Event
Visit Gore at AAAA to enhance mission success, survivability & safety
May 14, 2025 - May 16, 2025
Visit us at Booth 900 to experience our live demonstrations and discover how GORE® Cables and Materials enhance Army airframe and aviation systems. Reserve time now with a Gore specialist to discuss how we can help deliver solutions that support mission success, survivability and safety.
Press Release
W. L. Gore & Associates Joins Team FLRAA as a Wire and Cable Supplier for the U.S. Army’s Future Long Range Assault Aircraft Program
Posted May 13, 2025
NEWARK, Del./USA — W. L. Gore & Associates, a global leader in aerospace cables and materials, has joined Team FLRAA, bringing its technology to one of the U.S. Army’s most advanced modernization efforts.
Press Release
Bae Systems Honors W. L. Gore & Associates With a ‘partner 2 Win’ Supplier of the Year Award
Posted April 25, 2025
NEWARK, Del./USA — W. L. Gore & Associates today announced it received a Supplier of the Year award from BAE Systems’ Partner 2 Win program. Gore was selected from a pool of suppliers that delivered exceptional performance and contributions to support supply chain success for BAE Systems’ Electronic Systems sector in 2024.
FOR INDUSTRIAL USE ONLY
Not for use in food, drug, cosmetic or medical device manufacturing, processing, or packaging operations.
Contact Us
Related Products
Cables & Cable Assemblies
Sealants
Follow GORE® High Performance Aerospace Wires for Defense Aircraft