GORE® Microfiltration Media
Our semiconductor filtration membranes offer the best-available balance of retention and flow with proven resistance to extreme environments, assuring process purity and consistent high performance.
Consistent High Performance and Cleanliness in Semiconductor Filtration
With the highest retention and unparalleled flow, GORE® Microfiltration Media enables the manufacture of expanded polytetrafluoroethylene (ePTFE) membrane filters to improve productivity and increase processing yields.
Our membranes assure repeatable high performance, consistent quality and exceptional high cleanliness in critical filtration applications.
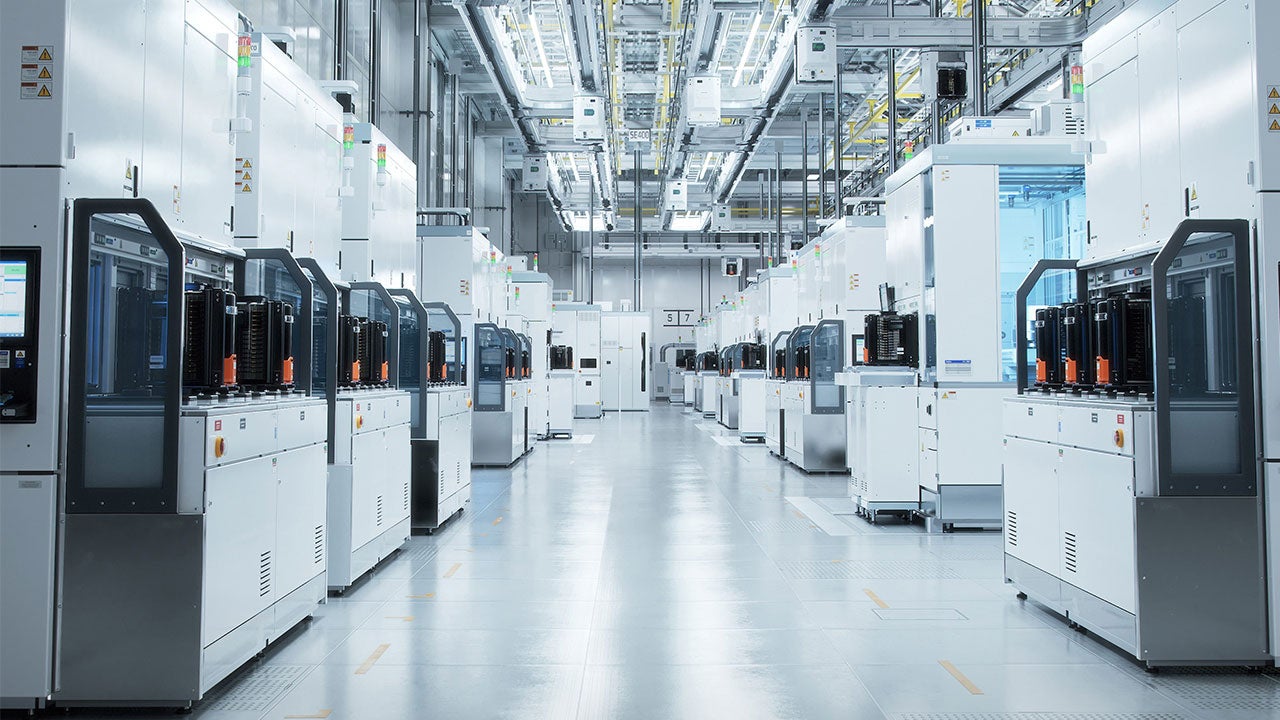
Improvements throughout Semiconductor Manufacturing Processes
With decades of unique materials science technology and in-depth application knowledge, Gore offers proven solutions that ensure cleanliness, durability and reliability.
Technical Information
Hydrophobic (ePTFE)
SM0-00002
SM0-00003
SM0-00005
SM0-00010
SM0-00020
SM0-00050
SM0-00100
SM0-00500
SM0-00A00
Hydrophilic (ePTFE)
HSM0-00010
HSM0-00020
HSM0-00050
HSM0-00100
HSM0-00500
HSM0-00A00
Laminate (Phobic/PP Net)
SM5-00010
SM5-00020
SM5-00050
SM5-00100
Explore More
FOR INDUSTRIAL USE ONLY
Not for use in food, drug, cosmetic or medical device manufacturing, processing, or packaging operations.
Prefer to Call?
Have questions or unique requirements?
Our experts are here to guide you.